KF5600/50 II | KF6700/50 II
High Speed & Productivity Vertical Machining Center
State-of-the-art Vertical Machining Center with High-speed and large work space. The Vertical Machining Center KF-II Series, designed by Hyundai WIA with years of expertise and the latest technology, maximizes productivity while maintaining rigidity and accuracy.
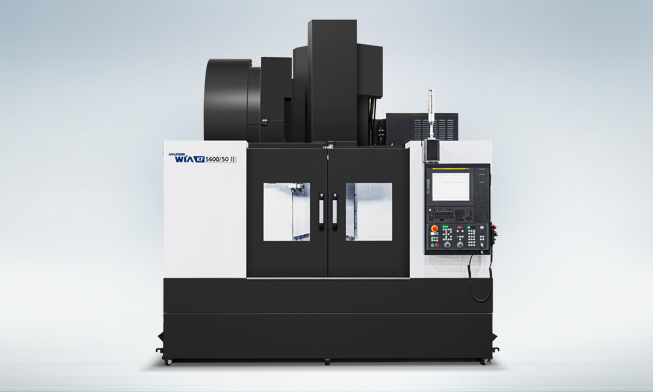
- High-precision machining by improved spindle quality
- High-speed roller type LM guide in all axes
- Enhanced chip processing capabilities by applying the upper-type conveyor
- Various motors and columns provided for customized machining
- Improved user convenience by applying the latest controller of FANUC
State-of-the-art Vertical Machining Center with High-speed and large work space
High-Precision Structure
Optimal Structural Analysis
KF-II Series is designed to have optimal structure through Hyundai WIA’s unique structural analysis. In particular, enhancement of bed and column’s rigidity makes excellent performance even in heavy duty cutting.
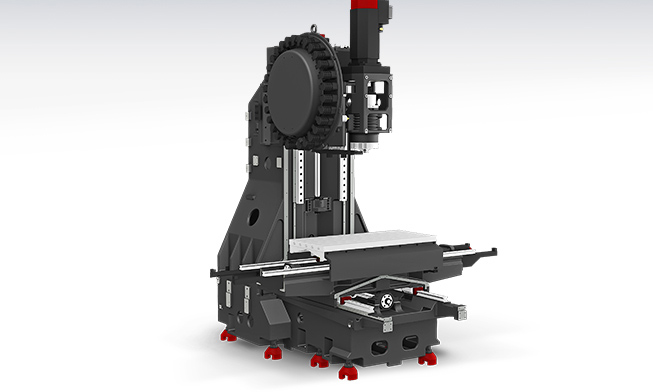
One Piece High Column (Direct Sp.)
One piece high column is provided as an option up to z-axis hegiht. This option helps to process bigger products such as rack housing.
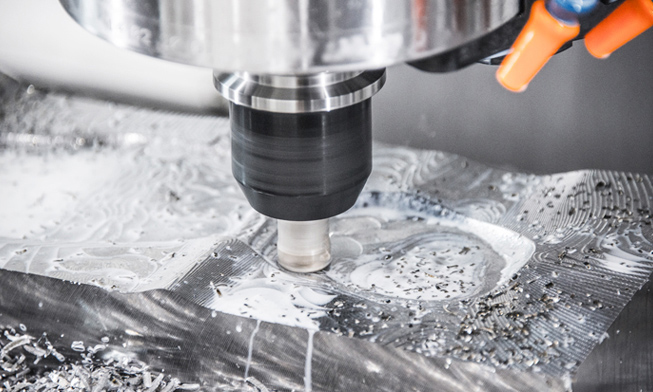
Guideway
High-Speed Roller LM Guideway
Linear roller guideways are applied to reduce non-cutting time and bring high rigidity. Each axis is directly connected to a highly reliable digital servo motor to provide high rigidity and minimal thermal displacement.
Improvement in Slide Cover
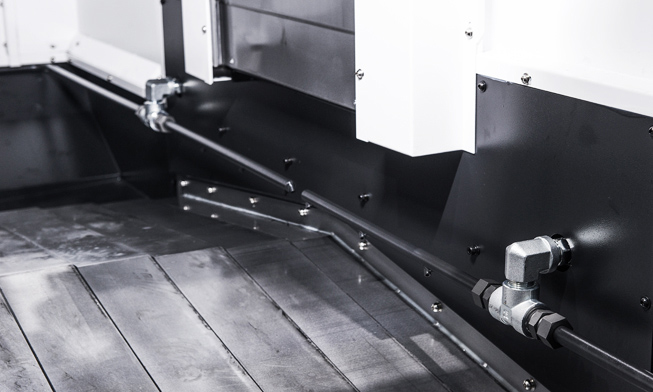
The increased slope of slide cover makes chip disposal easier and minimizes slide cover breakage.
Improvement in Slide Cover
The increased slope of slide cover makes chip disposal easier and minimizes slide cover breakage.
Double Anchored Ball Screw
The pretensioned ball screw minimizes the expansion and contraction according to the heat and further reinforces the rigidity by the double anchor support method. In addition, the coupling of the ballscrews and the highly reliable digital servo motors are connected by metal plate couplings, to reduce coupling breakage and backlash.
Increase in Durability of Z-axis ball screw
Lifetime of the bearing has been greatly increased by optimizing the spindle structure and lubrication method.
Nut cooling ball srew
Nut cooling ball screws on all axes decrease thermal displacement which enhances precision machining ability. (KF5600M/6700M)
Spindle
Direct Driven Spindle
The directly coupled spindle at a maximum revolution of 15,000rpm, allows high-speed processing. Additionally, the large diameter and the thickness of the spindle add to the stability of the machine.
Spindle Cooling (Over 10,000 rpm Std.)
The spindle cooling system minimizes thermal displacement which can happen during lengthy machining operations, and offers continued accuracy based on the thermal stability.
Through Spindle Coolant (20/30/70 bar)
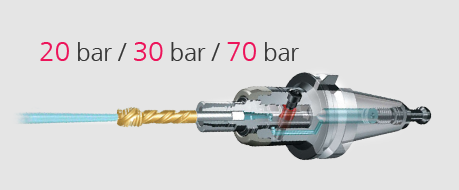
Through Spindle Coolant is exceedingly useful when drilling deep holes. It helps increase the lifetime of the tool, while decreasing cycle time. The improved quality of rotary joint prevents oil leakage.
ATC & Magazine
High Speed ATC
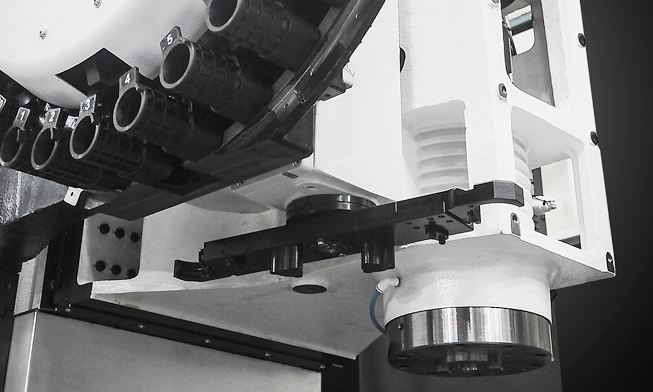
Position control through twin arm ATC on servo motors has been
improved drastically. In addition, tool exchanging has become
easier, reducing specific cutting time tremendously. Position control on the Twin Arm ATC has improved drastically. The twin arm ATC enables faster tool change and increased productivity.
Magazine
The tool magazine holds 30 tools as standard and 40 tools as an
option. Due to the wider selection of tools and the random tool
selection method, tool change time has improved.
Chip disposal solution & coolant unit
Interior Screw Chip Conveyor (Forward / Backward Rotation Function)
Dual screw type chip conveyors are located at each side of the bed which makes it convenient to remove chips. The interior screw and the chip conveyor operate at the same time and can be controlled separately at the time of prior consultation.
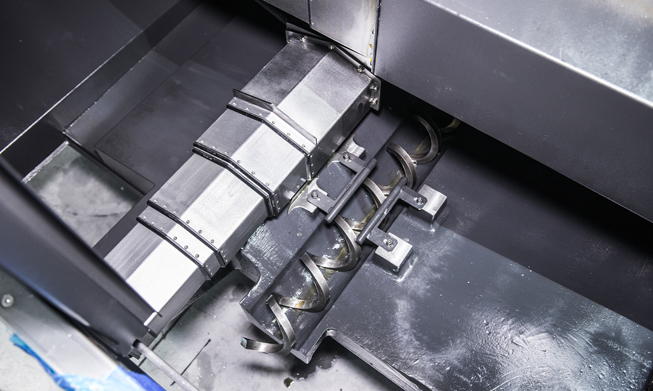
(Three screws for rear-type conveyor: 2 sides + 1 front). Furthermore, chip disposal capability significantly has been improved due to optional bed-flushing coolant.
NC Rotary table & hydraulic supply unit
Various shapes of products can be processed when using NC Rotary Table. In addition, 100 bar of high pressure hydraulic unit for the fixture increases the tightening power of the teeth.
Technical Specifications KF5600/50 II
Table Size [mm] | 1250×560 |
Max. Load Capacity [kg] | 1,000 |
Spindle Driving Method | Direct |
Spindle Taper | BBT50 |
Spindle RPM [r/min] | 8,000 |
Spindle Power [kW] | 22/11 |
Spindle Torque [Nm] | 353.2/143 |
Travel(X/Y/Z) mm | 1,100/560/520 |
Rapid Feed Rate(X/Y/Z) [m/min] | 36/36/30 |
Slide Type | LM |
No. of Tools | 24 |
Tool Change Time (Chip To Chip) [sec] | 5.5 |
Technical Specifications KF6700/50 II
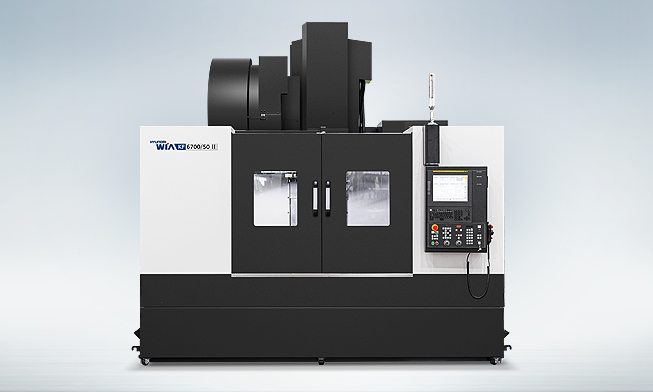
Table Size [mm] | 1500×670 |
Max. Load Capacity [kg] | 1,300 |
Spindle Driving Method | Direct |
Spindle Taper | BBT50 |
Spindle RPM [r/min] | 8,000 |
Spindle Power [kW] | 22/11 |
Spindle Torque [Nm] | 353.2/143 |
Travel(X/Y/Z) mm | 1,300/670/635 |
Rapid Feed Rate(X/Y/Z) [m/min] | 36/36/30 |
Slide Type | LM |
No. of Tools | 24 |
Tool Change Time (Chip To Chip) [sec] | 5.5 |